

Stress Corrosion Cracking (SCC): The growth of crack formation in a corrosive environment, SCC is typically found in highly stressed parts like landing gear or engine crankshafts. Historically, Citation X aircraft had some trouble with this corrosion in the wings, and Cessna has since added a regular inspection for early detection (called a Document 3). It can be tough to find, and whatever piece of metal is unlucky enough to have it is done for. Intergranular Corrosion: Not found often, Intergranular Corrosion can be devastating when it is discovered. Poor paint jobs or allowing paint to wear off and expose the metals underneath can often lead to a uniform surface attack. Uniform Surface Attack: The most common type of corrosion, Uniform Surface Attack is caused by exposing metal to oxygen in the air. Let’s consider each of these in more detail… The types of corrosion typically found on aircraft are Uniform Surface Attack Intergranular Corrosion Stress Corrosion Crevice/Deposit Corrosion and Filiform Corrosion. And corrosion is the object of a number of regular inspections from aircraft manufacturers. It’s arguably the most common discrepancy found during a pre-purchase inspection. With the different conditions under which an aircraft operates, it is not possible to completely avoid corrosion - but if detected and treated early, corrosion should not negatively impact the safety or longevity of an airframe.Īircraft corrosion refers to rust or material deterioration on any metal part of an aircraft. It can affect both the airworthiness of the aircraft and its resale value.
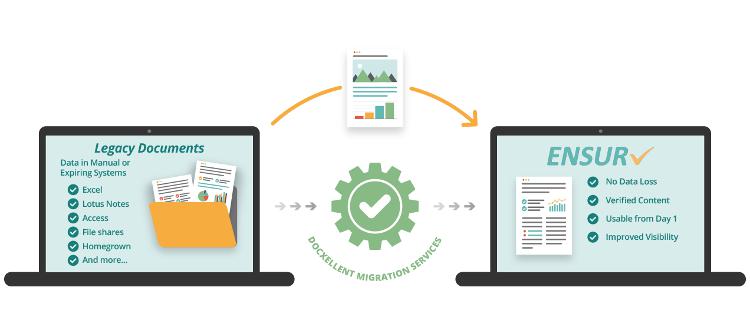
The presence of corrosion can be alarming if you don’t know much about it. But how can you avoid corrosion negatively impacting the value, safety and longevity of your jet…? Corrosion… It might well be counted as a four-letter word when it comes to aircraft, notes Rene Banglesdorf.
